Precision CNC Machining
Our unique business model employs highly skilled engineers in every aspect of the design and manufacturing phases. Their skill sets are deployed in design for manufacturability, project planning and the subsequent generation and execution of all necessary CNC programs to manufacture customer parts. From the receipt or creation of two dimensional drawing packages or three dimensional Solidworks models, our engineers employ a combination of manual and automatic programming tools to create customer part(s). The combination of their industry experience, problem solving abilities, and hands-on training enables Apogee to efficiently provide rapid, cost effective manufacturing solutions.
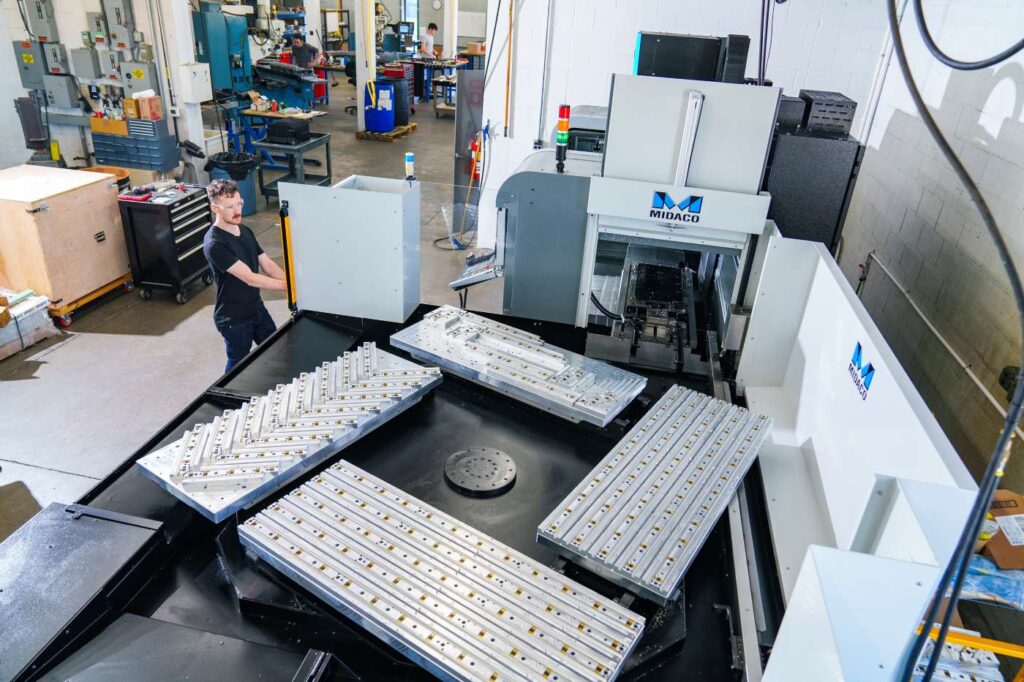
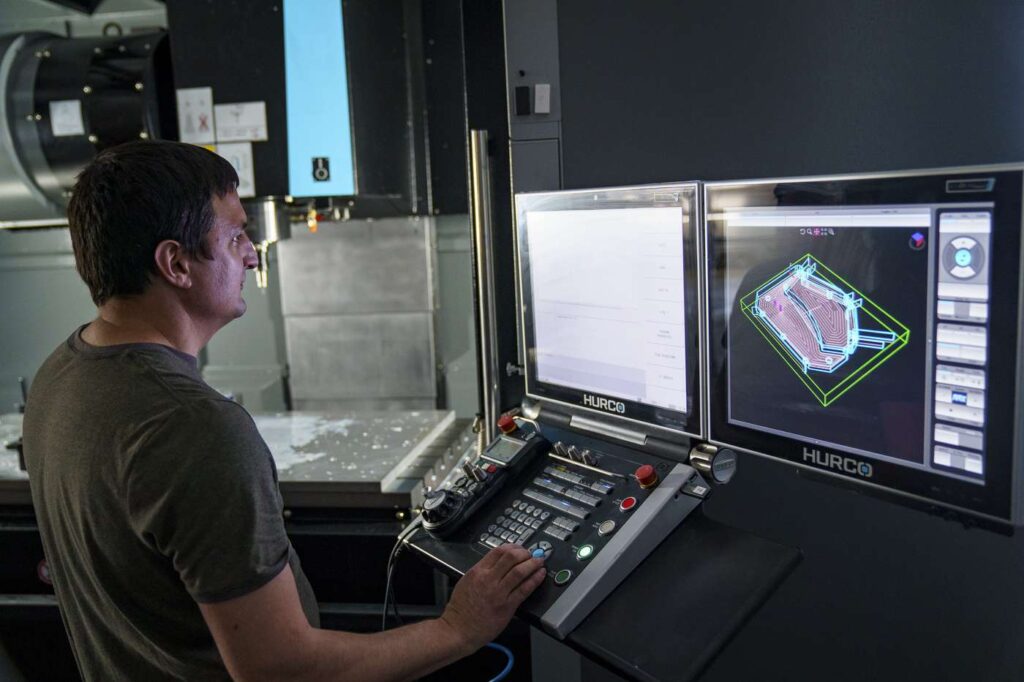
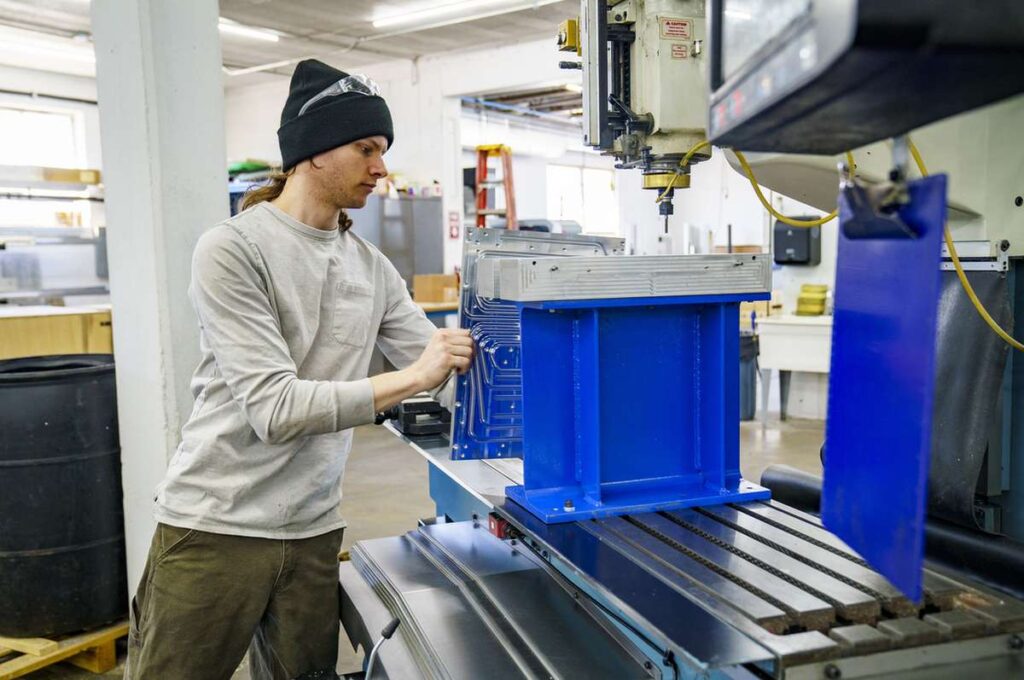
Apogee’s suite of manufacturing tools encompasses CNC bed mills, CNC vertical machining centers (VMCs), manual and automatic precision grinders, manual lathes, saws and hand tools to support a wide variety of customer projects. Our machine toolbox has always been customer driven. We listen to our customers and strive to remain cognizant of their current needs and prepared for their future needs. If you’d like us to invest in a unique capability, please contact us.
- CNC Bed Mills for Tooling Fabrication & Long Parts
- Vertical Machining Centers (VMCs) for Prototyping Through Production
- Grinding for High Precision Tooling
Spec Table
Standard: +/- 0.005 inches (0.127 mm),
Precision: +/- 0.001 inches (0.0254 mm)
Enclosed: 60″ L x 30″ W x 30″ H (1524mm L x 762mm W x 762mm H)
Open: 36 ft L x 40″ W x 30″ H (10.97m x 1m x 0.762m)
1 – 50,000 parts
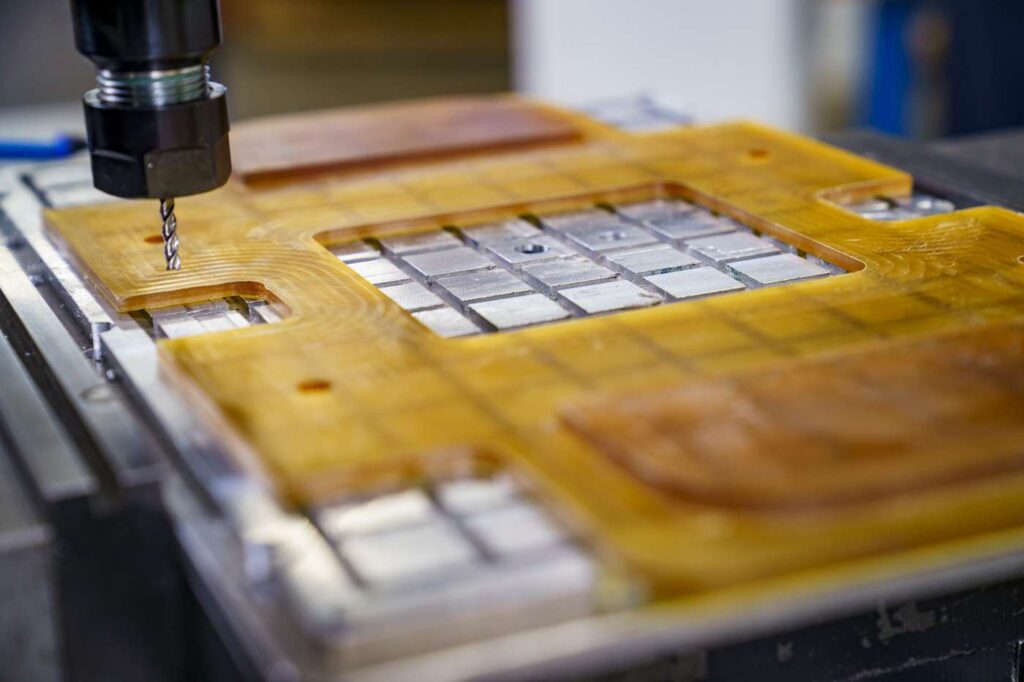
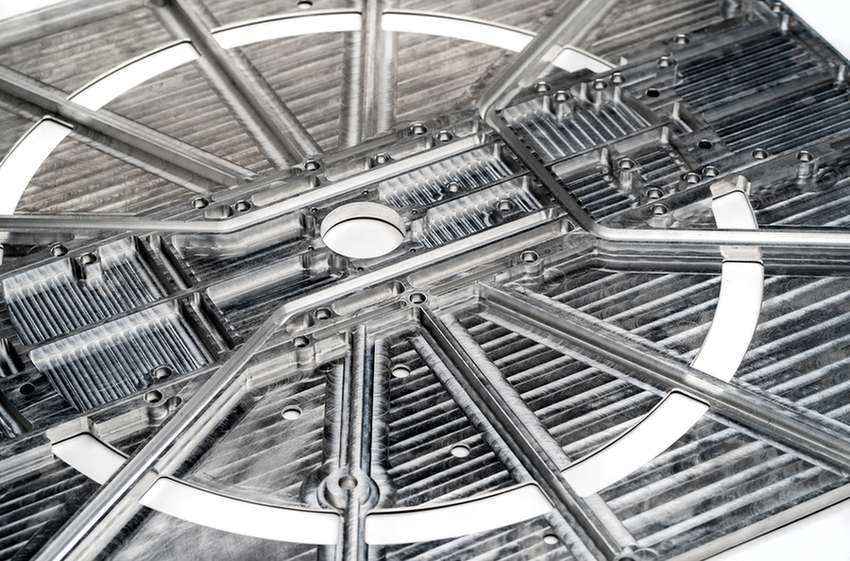
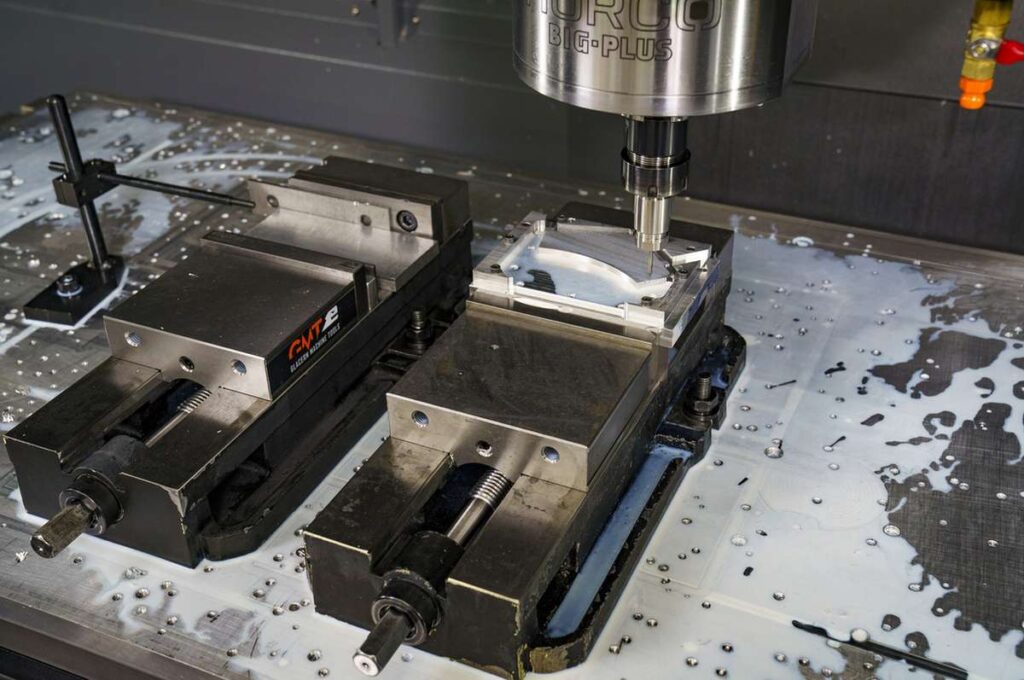
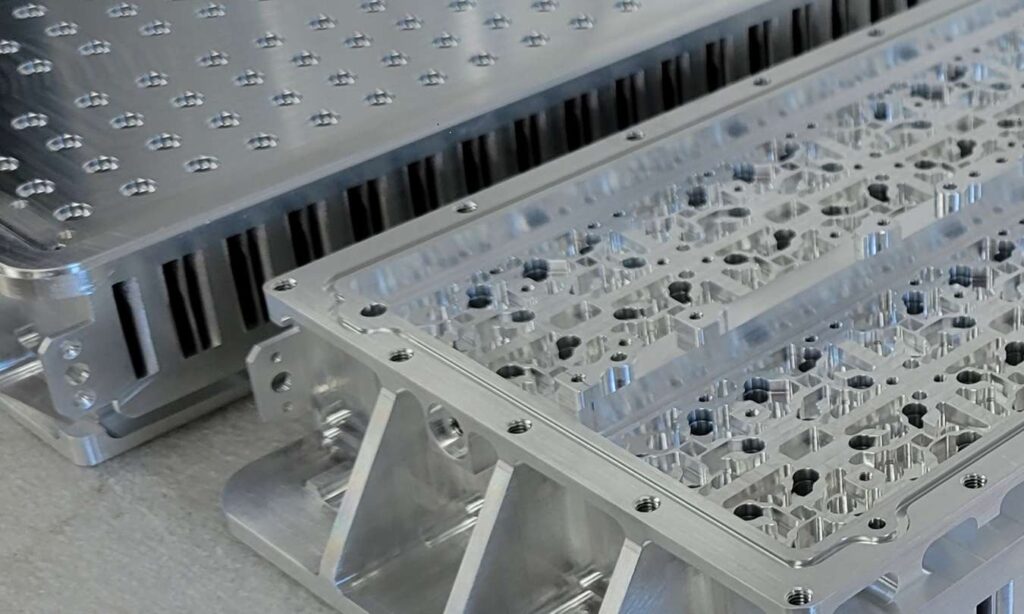
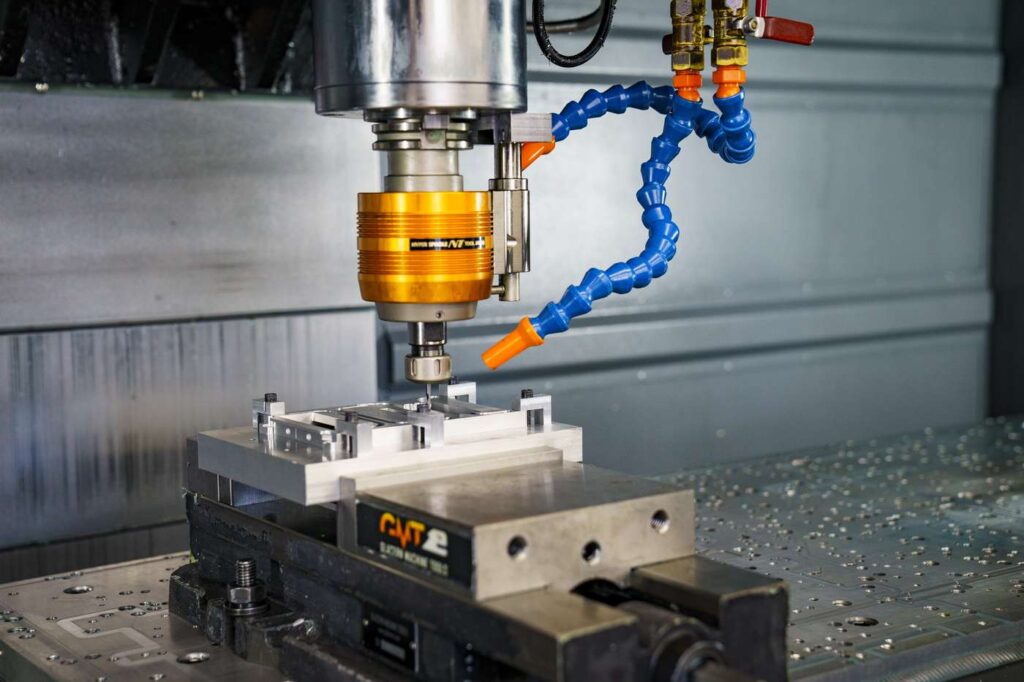
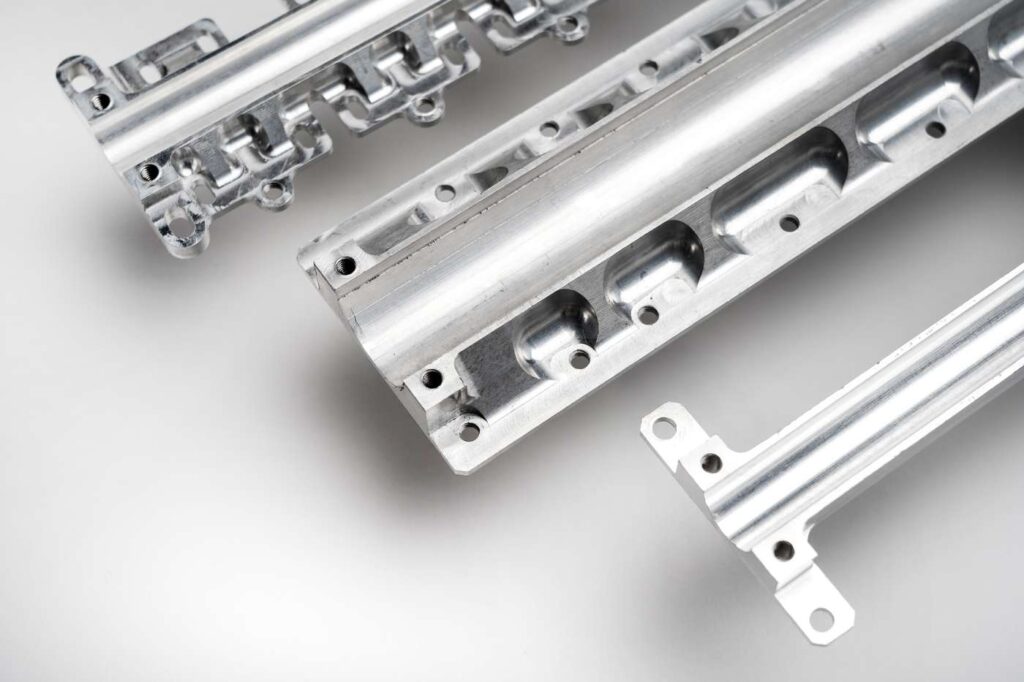
Apogee’s Machines
Our CNC bed mills are typically deployed in low volume production runs, tooling, ancillary operations for high volume production runs, and for very long length parts (up to 36 ft, parts that do not fit in an enclosed machining center). Apogee’s largest bed mills (Southwestern Industustries RX7s with ProtoTrak software) are nominally 60 inches in X by 21 inches in Y by 20 inches in Z and use advanced conversational programming. All of Apogee’s bed mills are well maintained and accurate to less than 0.001”. The open-air tables of these bed mills allow for versatile accommodation of larger and seemingly cumbersome form factors. Our assortment of bed mills are ideal for incredibly rapid setup and execution of customer’s quick turn requests. If you have an emergency machining request, please contact us.
For rapid material removal, high precision, improved surface finish, and volume production, Apogee’s machining centers can meet the most demanding customer requests. Our advanced CNC machining centers offer cutting edge performance resulting in higher precision and increased production rates compared to our bed mills. All of our machining centers leverage manual, conversational, CAM generated and g-code programming enabling quick setup and rapid turn around, and are deployed in low to high volume production (up to 50,000 parts). Apogee’s largest VMC (Hurco VMX 6030i with the Latest WinMax software) is 60 inches in X by 30 inches in Y by 24 inches in Z and uses advanced conversational programming. Most of Apogee’s VMC’s are capable of 12,000 rpm and are well suited to production. With accuracy and repeatability less than 0.0004”, Hurco machines are well suited to the stringent needs of the Aerospace customers as well as other demanding markets.
High volume production is improved through a variety of tactics that increase efficiency by decreasing run-time. Depending on the application, Apogee deploys spindle speeders, custom designed tools, volume capacity holding fixtures and clamps, pallet changers and duplicate operations. A variety of spindle speeders (up to 65,000 rpm) can be used to boost micro-tool feed rates on parts with intricate features. Apogee’s custom designed cutting tools combine milling, drilling, and deburring operations thereby reducing the number of tool changes. Several of our machining centers are equipped with high pressure (up to 1000 psi) coolant through spindle (also known as coolant through tool) systems for high speed, deep hole drilling, rapid material removal and very deep pocket machining. High volume production holding fixtures are designed to maximize the number of components simultaneously loaded into a machine. This optimization significantly increases a machine’s efficiency by reducing the number of tool changes and the frequency of machine interruption. Advanced clamping mechanisms further reduce part loading and unloading time. Our Midaco Four Pallet Rotary Pallet Changers enable round-the-clock production through the automatic loading and unloading of parts within a 50 inch x 20 inch x 20 inches (X, Y, Z) envelope. We also build redundant fixturing for multiple machines to increase capacity as needed.
Apogee creates custom CNC programs using a variety of methods depending on the project. CNC programs are created manually at the machine terminal using data from a printed drawing for simple and quick operations like hole drilling and basic rectangular milling. CNC programs for complex contours are created in Computer Aided Machining (CAM) software. Apogee used CAMWorks for these applications, which seamlessly integrates with SolidWorks. Conversational programming is deployed for parts and geometry that are mildly complex. Hurco’s Winmax Software and Southwestern Industries’ Prototrak Software are used extensively at Apogee for offline (typically on a laptop) programming or at the machine terminal. Conversational programming is incredibly efficient at generating programs with a limited complexity. Both Winmax and Prototrak enable programming directly from imported 2D or 3D geometry. The extensive experience and professional training of our team enables Apogee to develop cost-effective CNC programs for each customer project.
Contact Us
"*" indicates required fields