Tooling Design
Tooling Design is a critical and specialized area of manufacturing engineering which comprises the analysis, planning, design, construction and application of tools, methods and procedures which either enables a product to advance through production, or increases existing manufacturing quality and/or productivity.
Apogee’s team of experienced engineers support customer projects through every phase from prototype development through high volume production. Our efficient design solutions, whether applied in the development and fabrication of customer tooling or applied in-house to create custom manufacturing solutions, are tailored to the specific needs of each project and budget.
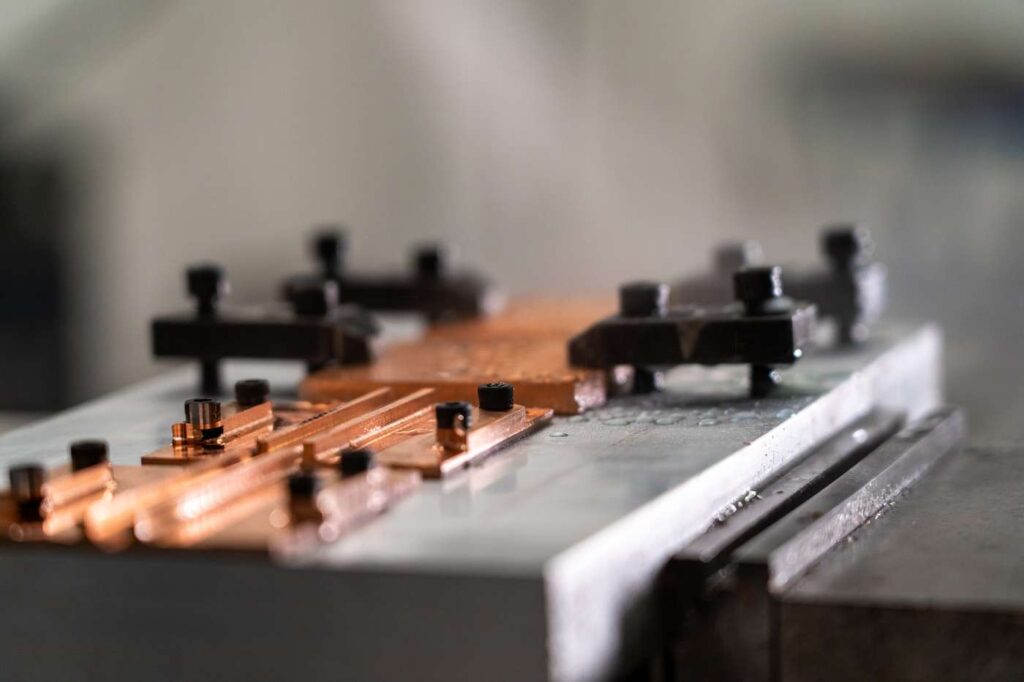
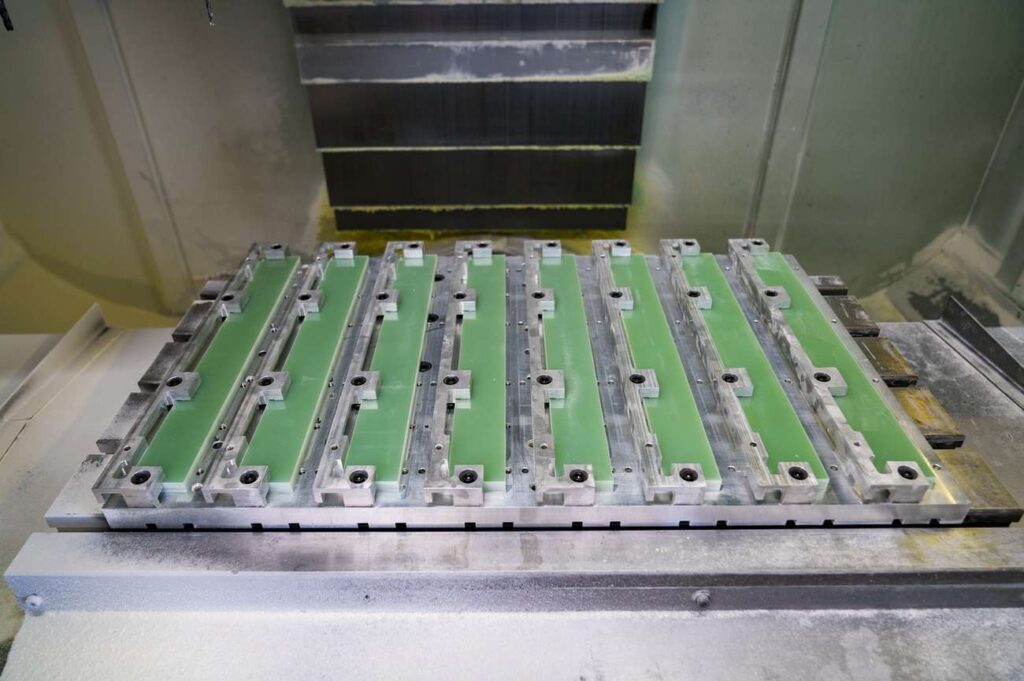

Tooling Design for Customer Applications
Successful tooling design and deployment requires clear communication and understanding between the operator and the design team. Apogee’s extensive hands-on experience enables clear and consistent communication with all levels of our customers, from operators to stakeholders. We understand the expectations of operators for loading and unloading parts with ease, while providing consistent tool performance as required by quality assurance, within the budget expectations of project managers.

Design Process
Design complexity, materials selection, ergonomics, weight, form, power consumption, batch sizing and cost constitute only a subset of the many considerations behind the creation of a successful tool. Manually operated hand tools are ideal for proof-of-concept and low volume prototypes because they satisfy customers’ demands for a quick, cost-effective tool with minimal investment. Fully automated and semi-automated tools with electronic, pneumatic or hydraulic actuated components controlled with Programmable Logic Controllers (PLCs) are ideal for high volume repetitive processes, combining synergistic processes for improved production rates, and/or instances when manual labor is cost prohibitive.
Apogee designs custom soft and hard tooling solutions in a wide variety of materials. Soft tooling is commonly manufactured from plastic, phenolic and aluminum, while hard tooling commonly utilizes steel, stainless steel, pre-hardened 4140 tool steel or in-house heat treated A2 tool steel. Our engineering team will carefully select the material, tooling type and type of manufacturing processes to support your end application as well as provide clearly written user instructions and demonstrations as needed.
Apogee Tooling Design Examples:
Custom designed benders for tight tolerance and critical applications. Simple and complex two and three dimensional paths for the bending of copper, aluminum, stainless steel, steel, and titanium tubing.
Application Examples:
- Aluminum Ammonia Constant Conductance Heat Pipes for Satellite Thermal Control
- Embedded Copper Tubing or Heat Pipes for Aluminum or Stainless Steel Cold Plates
- Single and Two Phase Pumped Loop Tubing
Thermal, Acceleration, Mechanical, Fatigue, Life Cycle
Application Examples:
- Turn-Key Thermal Performance Test Fixtures Including Heaters, Cold Plates, Controls and Instrumentation
- Centrifugal Acceleration Qualification Test Fixtures for Heat Pipes in High G Applications
- Fatigue Qualification and Acceptance Testing Fixtures for Flexural Assemblies
Go/No Go Gauges, Mock Assemblies, and Alignment
Application Examples:
- Precision Geometric Inspection Fixtures for Custom Parts
- Keep-in-Volume Inspection Acceptance Fixtures for Complex Bent Tubing for Spacecraft
- Datum Feature Simulators for Acceptance Inspection of Sheet Metal Formed Parts
- Go/No Go Gauges for Pipe Weld Reinforcement
Holding, Sawing, Machining, Turning, Swaging, Painting, Soldering, Bonding, Assembly, Packaging
Application Examples:
- Block-Heat Pipe-Fin Plug & Play Soldering Fixtures for Electronic Cooling
- Custom Hardened Steel Rotary Swage Pipe Dies
- Pipe End Closing Spin Dies
- Length Setting Fixtures for Semi-Automated Tubing Saws
Legacy Tool Optimization, Refurbishment, and Component Replacement
Tool maintenance and upgrading are also an integral part of manufacturing. Apogee offers tool design for upgrades, refurbishment and replacement for all your existing tooling. These services include functional optimization, reverse engineering and fabrication of broken components, and modifications to accept design changes or new parts. We will gladly visit your facility to ensure our complete understanding of your tooling needs for all applications.
Sheet Metal Forms, Shears, Punches and Dies: In-House Heat Treated for Long Life and Durability
Application Examples:
- Punch and Die Set Rebuilding and Sharpening Services
- Reverse Engineering for Old/Unsupported Punch and Die Sets
- Custom Threaded Insert and Pin Installation Tools (Dowel Pins, Keensert, Helical, LongLok etc.)



Tool Design for Use In-House
Apogee leverages its tool design prowess in-house to create custom workholding solutions that increase the efficiency of the CNC machining, manufacturing and inspection processes on a daily basis. We design and build custom fixture plates, vacuum tables and clamps as well as precision ground blocks and jigs. Our effective tooling concepts and continuous tooling optimization increase the efficiency of the overall manufacturing process, saving customers time and money.
ContACT uS
"*" indicates required fields